Piping Stress Analysis (Flexibility Analysis) is an important design function that designers and engineers, in nearly all of the engineering departments associated with and affected by Piping Design, should be aware of Piping Stress fundamentals.

Chemical Tanker Piping Network (as example of high-density piping area). Source: https://navlib.net/-tanker-vocabulary/)
Some bullet points to understand the importance of Piping Stress Analysis:
· The Piping Stress Analysis is the mechanical integrity assurance behind of the issue for construction (IFC) isometric drawings and functions as a design basis the piping fabrication.
· The IFC isometric drawing is the fundamental document for piping fabrication and installation.
· The Piping Stress Analysis shall guarantee that mechanical stresses in the piping and the piping loads generated on supports, vessels and equipment are within allowable limits.
· Engineering and Construction companies should provide a short course or at least an obligatory training document to show, to non-stress specialists, the fundamentals and the consequences of not considering Piping Stress principals in their disciplines. Something as simple as a thermal expansion calculation estimate could prevent field fixes due to operating clashes or instrument/electrical connection binding. This should include most engineering disciplines, construction and even the client.
Now let’s look to some examples:
Suppose that we require to design a plant with:
1) High temperature and pressure piping systems.
2) Numerous alloy and stainless-steel piping (more expensive than carbon steel pipes).
3) Heavy wall (thick) piping due to high pressure and temperature.
4) Some modular designs due to space restrictions or to save field fabrication and construction time.
A common perceived upfront savings by other groups, especially for a lump sum project, plant equipment and vessels may be designed to their minimum allowable standards, including the flanges or piping connecting points.
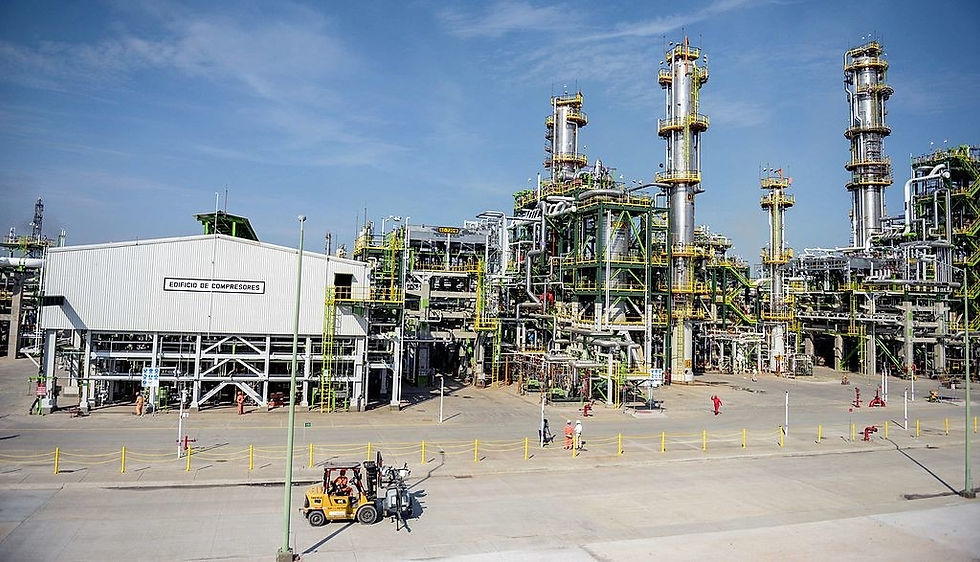
Tula Refinery, México. (Source: Presidencia de la República Mexicana. https://www.flickr.com/photos/presidenciamx/23507774012/)
The problem is that if the equipment (and vessels) are designed to the minimum required and given that the piping systems are thick and high piping temperature, then the piping will generate large loads. This in turn will require an increase in piping flexibility, resulting in changes in direction and new or more piping reroutes. This yields more elbows and more piping runs. For alloy and stainless steel piping the expensive material costs will quickly negate the initial perceived savings both in equipment and vessels.
Additional complications arise when there is a high density plot space for the equipment and piping, as in modular designs, a change of piping routing to increase flexibility can be quite traumatic during the detailed engineering phase. The proximity to other piping systems and structures may keep snowballing to require additional modifications and so on.

PSEEZ’s Petrochemical Complex, Asaluyeh (Source: https://www.tasnimnews.com/fa/media/1394/11/10/984201/)
In the end, the introduction of more piping routings, more direction changes and more complex piping arrangements around equipment and vessels could increase the maintenance problems and can even increase safety risks by reducing alternative personal escape routes. This would mean that the overall plant design could have approval problems by the plant owner or client.
From a process perspective the design of the pressure equipment (pumps, compressors or blowers) requiring these additional elbows and piping runs, the additional pressure losses associated with these incremental changes could cause the pressure equipment to be designed with insufficient discharge pressure. Again leading to redesign or increased equipment cost.
Reaching this point is when we can understand the problems real magnitude. When the piping stress specialists evaluates and begin to request changes to the piping design, the vessels and equipment are already designed, purchase orders to manufacturers or suppliers in place, and maybe are even under construction. The consequences are that the expenses and even the plant viability can be in jeopardy. Similar examples of piping stress fundamental problems can involve other disciplines such as instrumentation and can affect construction.
Many negative outcomes can result as a consequence of designing and installing piping without taking in account basic piping stress analysis principals. The recommendations that the piping stress engineers (or even just one stress engineer screening initial piping layouts and equipment specifications) will positively contribute to the initial phase through the life of the of the project.
Article by Antonio (Tony) Martínez / Piping Stress Engineer
(Edited by Bob Zimmerman, Vice President, The Piping Stress International Association)